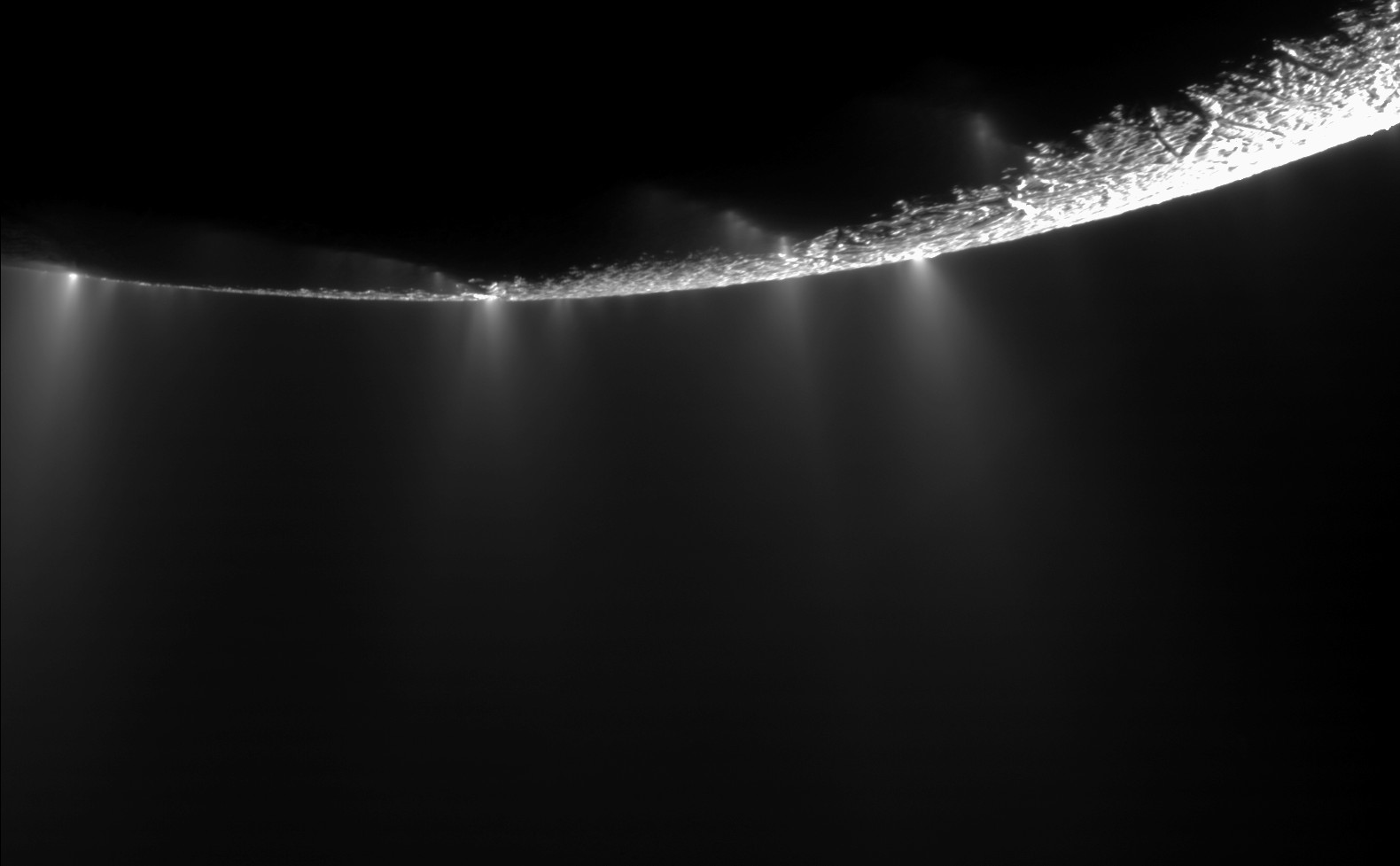
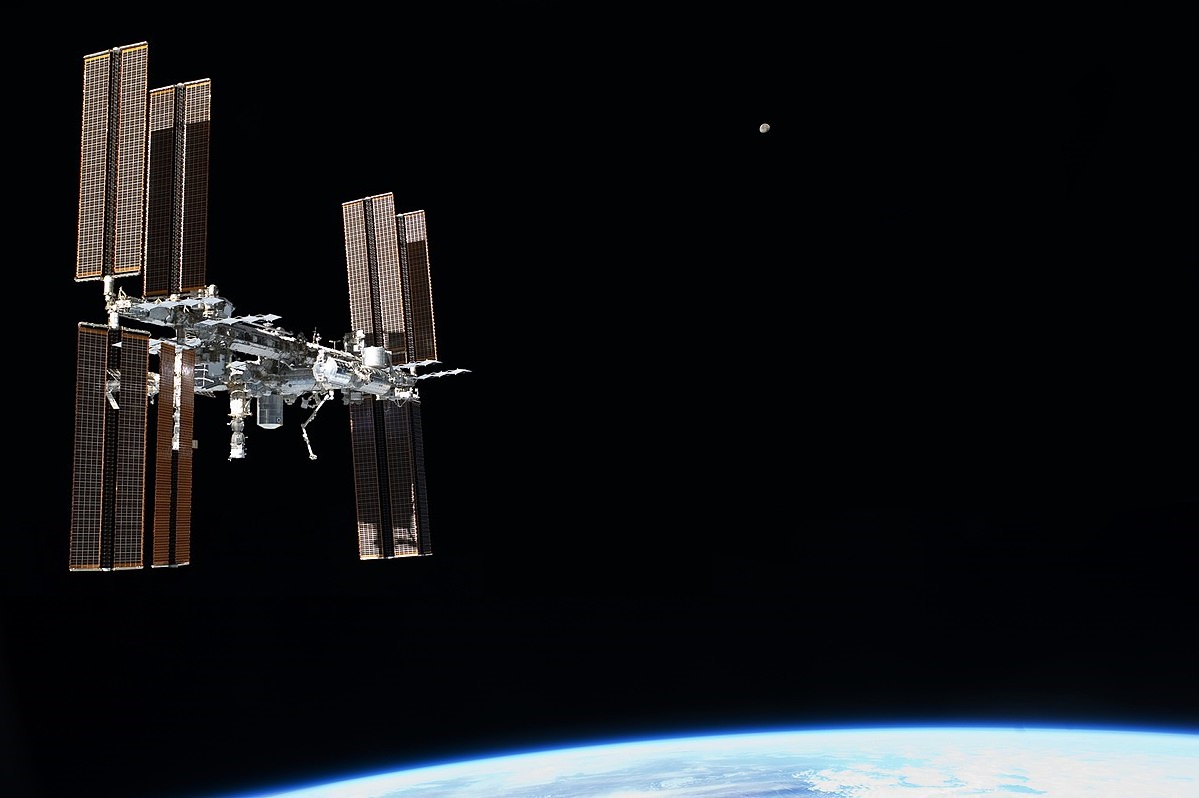
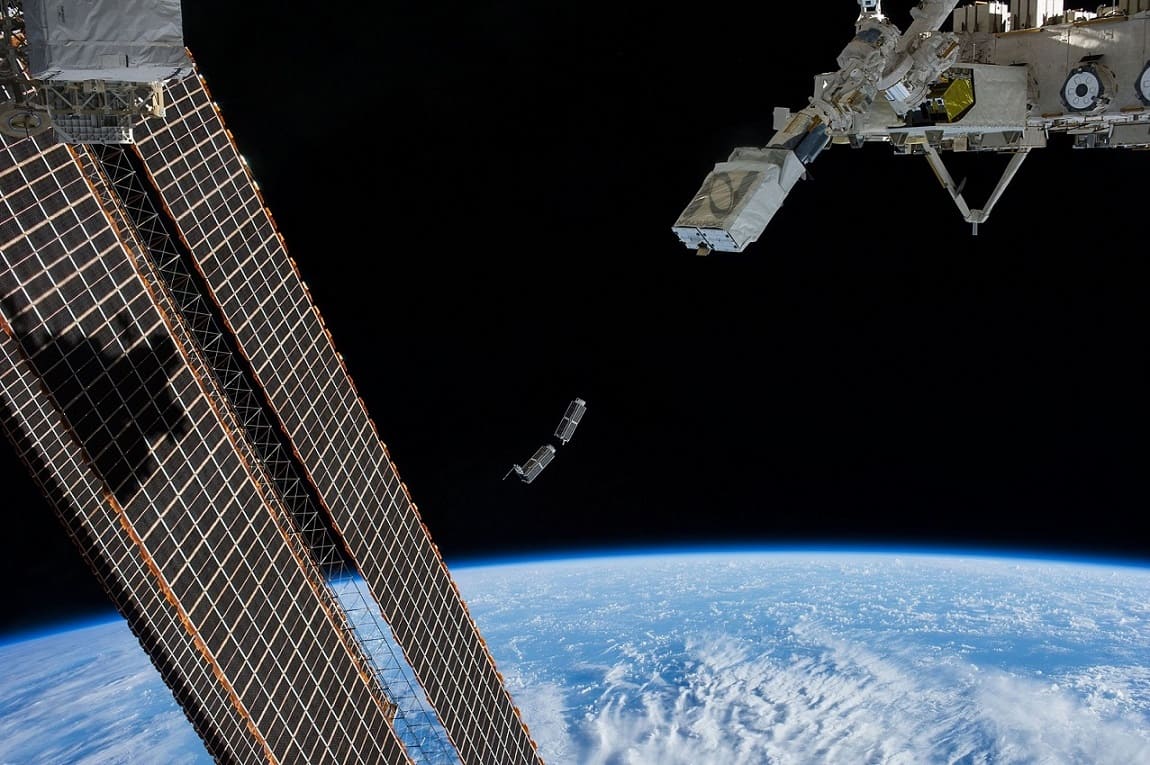
Manufacturing for the future, on Earth and in space
Space-based manufacturing of materials poses numerous advantages for U.S. space exploration and utilization. Launch costs may be significantly reduced by launching raw materials for space-based fabrication and structures that are too large for transport may be fabricated in situ. The freeze-casting technique is simple, scalable, cost-effective, and employs easily obtained materials. Moreover, complex manufacturing equipment is unnecessary and the range of producible, near net-shaped porous materials is nearly limitless. To date, the freeze-casting technique has been utilized to fabricate porous polymer, ceramic, metal, and composite materials. The large number of materials that have already been fabricated using this technique is illustrative of the fact that the principles governing freeze-casting are not strongly dependent on the composition of the materials (or chemical interactions), but rather on the fundamental, physical nature of the solidification process. The freeze-casting technique has the potential to extend and sustain human activities beyond low-Earth orbit by providing a method to manufacture structural and functional materials in space, thus increasing the reliability and safety of access to space while also decreasing overall costs.
The solidification of metals and alloys in microgravity has been studied for over thirty years. The research offers significant insight into the physical properties governing the freeze-casting process. However, solidification of slurries is a bit more complex. Indeed, despite major advancements in the freeze-casting technique, the underlying principles that govern solidification behavior are not well understood. Current research approaches strive to improve the mechanical and functional properties of resulting porous materials, but these attempts are limited by our current knowledge base.
A major advantage of the freeze-casting technique is that it inherently allows for the adjustment of microstructural properties through the manipulation of solidification conditions. This is significant because it means that mechanical and physical properties of final products may be tailored to suit desired applications simply by modifying the conditions of solidification, e.g. solidification temperature, solid content of the suspension, particle size, just to name a few.
Of course, there are some limitations, but in principle, since the ice dendrites serve as templates for pores in the final product, learning how to precisely control their growth is paramount to achieving a desired final structure. Microgravity research helps us to better understand the fundamental processes at work, which can lead us to the development of improved terrestrial fabrication techniques.
In freeze-cast materials, ice lenses are defects that form during solidification and compromise a resulting material’s compressive response. In geology, ice lensing is studied as the mechanism responsible for frost heaves. Similarly, for planetary scientists, ice lenses initiate geomorphic events that hold insights into climate history. Our parabolic flightwork provided evidence that gravity may contribute to ice lens development in freeze-cast materials (Fig. 1).
Fig. 1. Longitudinal cross-sections of a sintered TiO2 sample sintered from a 20 wt% TiO2 aqueous suspension directionally solidified under terrestrial conditions, showing periodic ice lenses perpendicular to the freezing direction. White areas represent sintered TiO2 particle walls and dark areas represent pores, templated by individual ice lenses (red arrows). The ~70 mm thick white band at the bottom of the image is the bottom of the sample, consisting of densely sintered TiO2, which was in contact with the freezing substrate.
For the CubeSat mission, we will freeze salt water solutions and aqueous particle suspensions. We anticipate that the collection of temperature and image data during solidification will offer important insight into ice segregation patterns observed in oceans, soil, and on planetary surfaces, while also helping us to better understand the formation mechanisms of ice lens defects in freeze-cast materials.
Fabricating materials using ice
Freeze-casting was first used as a materials processing technique by NASA in 1954 [1]. The original work consisted of bulk freezing aqueous particle suspensions. After freezing, ice removal, and sintering, near net-shaped refractory materials were obtained (Fig. 2). Then, in the late 1970's freeze-casting was used in the food processing industry to produce imitation meat [2]. It wasn't until the early 2000's that materials scientists rediscovered it [3-5], this time, assigning ice the additional role of inducing particle assembly to form walls surrounding elongated, aligned pores. The basic procedure is still very simple, the only major change being the induction of a temperature gradient during freezing.
In general, the freeze-casting process consists of four steps. First, we mix a suspension that contains particles in water (a). The second step is "solidification". For this step, we place the suspension on a cold plate. Ice crystals nucleate at the bottom and begin to grow toward the top. As they grow, they push particles out of the way (b). These particles form an "accumulation region" ahead of the ice crystals (c). As the ice crystals continue to grow, the number of particles within the accumulation region increases. Eventually, particles are incorporated within interdendritic space. Once the suspension is completely frozen (d), we remove the ice using a freeze-dryer (e). As shown in (e), the particles stay where they were, and the ice crystals are replaced by pores. At this point, the material is very fragile. We "sinter" the particle matrix (f) so that the particles bond together.
A more detailed description of the freeze-casting process can be found here
[1] Maxwell, W.G., RS; Francisco, AC, Preliminary investigation of the'freeze-casting'method for forming refractory powders. 1954.
[2] Kim, Myung, Lugay, Castro, Fibrous protein materials, United States Patent No. 4,001,459, Washington, DC: U.S. Patent and Trademark Office. Jan. 4, 1977.
[3] Madihally, Matthew, W.T., Porous chitosan scaffolds for tissue engineering. Biomaterials, 1999. 20: p. 1133-1142.
[4] Schoof, H., Fischer, A., Heschel, I., Rau, G. Dendritic ice morphology in unidirectionally solidified collagen suspensions. Journal of Crystal Growth, 2000. 209: p. 122-129.
[5] Fukasawa, T., Ando, M., Ohji, T., Kanzaki, S. Synthesis of porous ceramics with complex pore structure by freeze-dry processing. J. Am. Ceram. Soc, 2001. 84[1]: p. 230-232.
Visit our press section to read more about our projects
We conducted the first microgravity freeze-casting experiments during three parabolic flight cam-paigns (2013, 2014, and 2016) with NASA’s Flight Opportunities Program (FOP). Our initial microgravity results provided evidence that gravity influences the microstructural templating process during solidification (see below). Further testing, in a longterm microgravity environment, is needed for generalization.
Scotti, K. L., Northard, E. E., Plunk, A., Tappan, B. C., & Dunand, D. C. (2017). Directional solidification of aqueous TiO 2 suspensions under reduced gravity. Acta Materialia, 124, 608-619. [pdf]
In collaboration with the University of Illinois, we are sending freeze-casting to Low Earth Orbit! At Northwestern, we are designing the experiment and payload, while UIUC (CubeSat Project) is building the satellite. This project is funded by NASA's Office of Education through the Undergraduate Student Instrument Project. Our anticipated launch date is late 2018.
Once in orbit, we'll collect image and temperature data while freezing aqueous suspensions of silver coated glass beads and salt water solutions. Whereas we were limited to freezing very quickly during our parabolic flight work, the CubeSat platform will allow us to test a range of freezing velocities.
As part of NASA's Materials Lab Open Science Campaign, we'll be sending a freeze-casting experiment to the ISS in 2022! For this "sample-return" mission, we will be using the PFMI apparatus designed by NASA Marshall Space Flight Center.
After samples are solidified on the ISS, they will be returned to Northwestern, where we will conduct microstructural investigations. We hope to learn more about the effect of gravity during solidification by comparing microstructures of samples solidified on the ISS to those solidified under normal terrestrial conditions (i.e., the lab).
Press Inquiries: KristenScotti@u.northwestern.edu
A NASA mission is sponsoring undergraduate research to test space-based manufacturing
Northwestern students lift off with NASA on a zero-gravity quest for efficient solar power technology.
The student team will freeze-cast materials for solar cells
CubeSat Mission
Northwestern University
CubeSat Mission
Northwestern University
CubeSat Mission
Northwestern University
CubeSat Mission
Trinity College
CubeSat Mission
University of Illinois
CubeSat Mission
Bradley University
CubeSat Mission
Northwestern University
CubeSat Mission
Northwestern University
CubeSat Mission
Northwestern University
CubeSat Mission
Northwestern University
CubeSat Mission
Northwestern University
CubeSat Mission
Northwestern University
CubeSat Mission
Northwestern University
CubeSat Mission
Northwestern University
CubeSat Mission
Northern Illinois University
CubeSat Mission
Northwestern University
Parabolic Flights
Northwestern University
Parabolic Flights
Northwestern University
Parabolic Flights
Northwestern University
Parabolic Flights
Northwestern University
Parabolic Flights
CubeSat Mission
ISS Mission
Northwestern University
CubeSat Mission
Northwestern University
Medill School of Journalism
CubeSat Mission
Northwestern University
Medill School of Journalism
Parabolic Flights
CubeSat Mission
ISS Mission
Northwestern University
CubeSat Mission
Northwestern University
Medill School of Journalism
This work is supported by grants from: NASA Flight Opportunities Program, NASA Office of Education, NASA's Science Mission Directorate, NASA's CubeSat Launch Initiative, NASA’s Physical Sciences Research Program, Northwestern University Office of Undergraduate Research, and Institute of Sustainability and Energy at Northwestern (ISEN)
spaceice@u.northwestern.edu